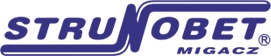
LSW 2 - 54 industrial line for the production of spun cast concrete poles in non-collapsible molds
The LSW 2 – 54 industrial line is an example of a technological line from the Strunobet company’s offer for the production of prestressed energetic spun cast concrete poles (type E) in non-collapasible molds. Strunobet offers the entire family of LSW industrial lines with various capacities and expansion possibilities.
Over 20 years of experience
The Strunobet company has over 20 years of experience in industrial projects and the development of production lines for prestressed spun cast concrete poles in non-collapsible molds in Poland and on foreign markets, e.g. Africa.
We are focused on development and new markets. We’re excited about this!
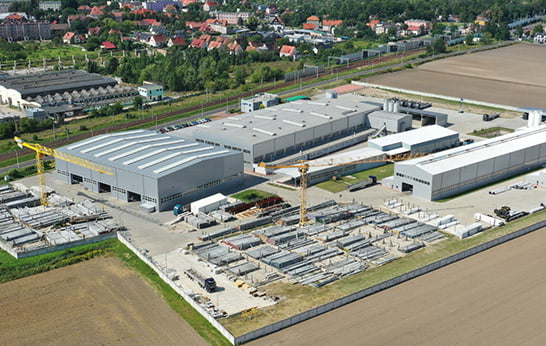
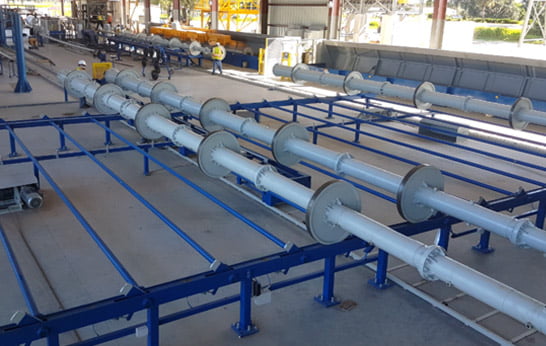
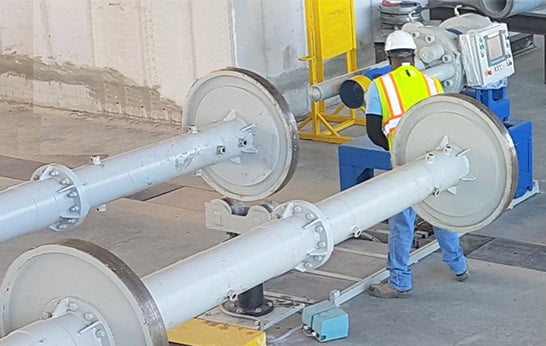
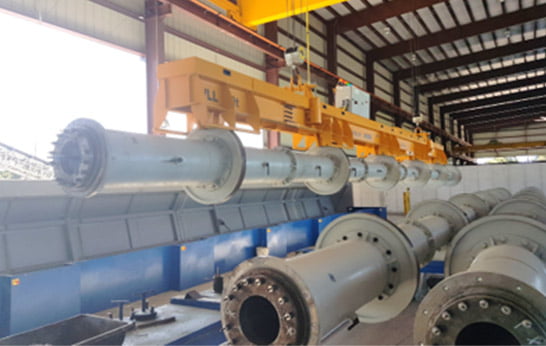
Worldwide delivery and customer support.
Strunobet-Migacz Sp. z o. o. provides industrial production lines for clients from all over the world. If the customer wants, we can send our poles by sea to carry out strength and quality tests.
Installation and commissioning of the new line at the Client’s site is carried out by our qualified team.
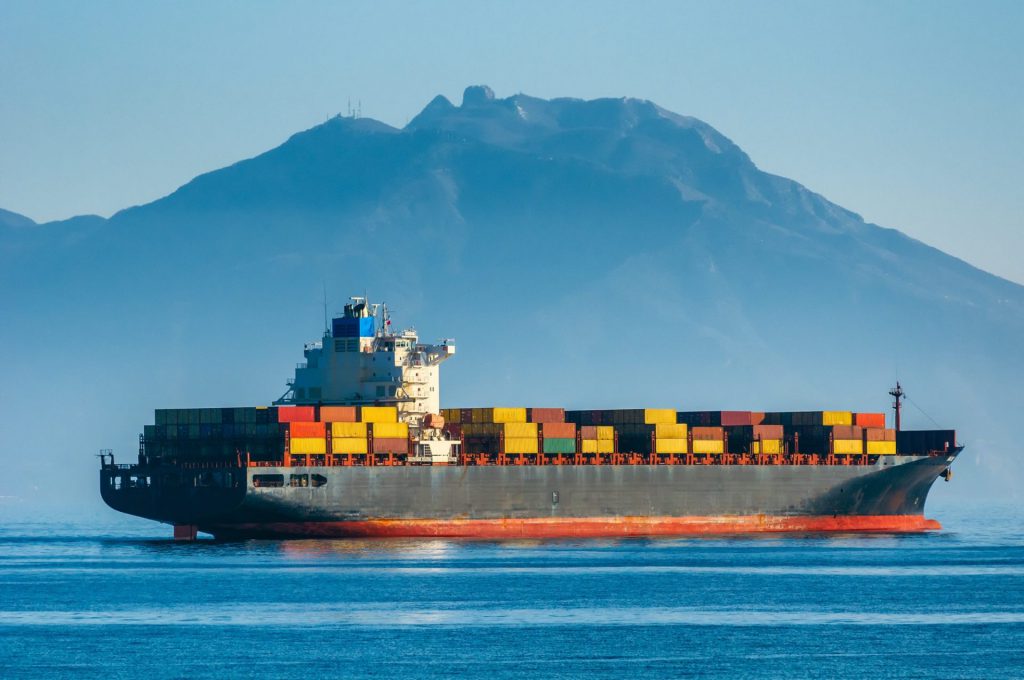
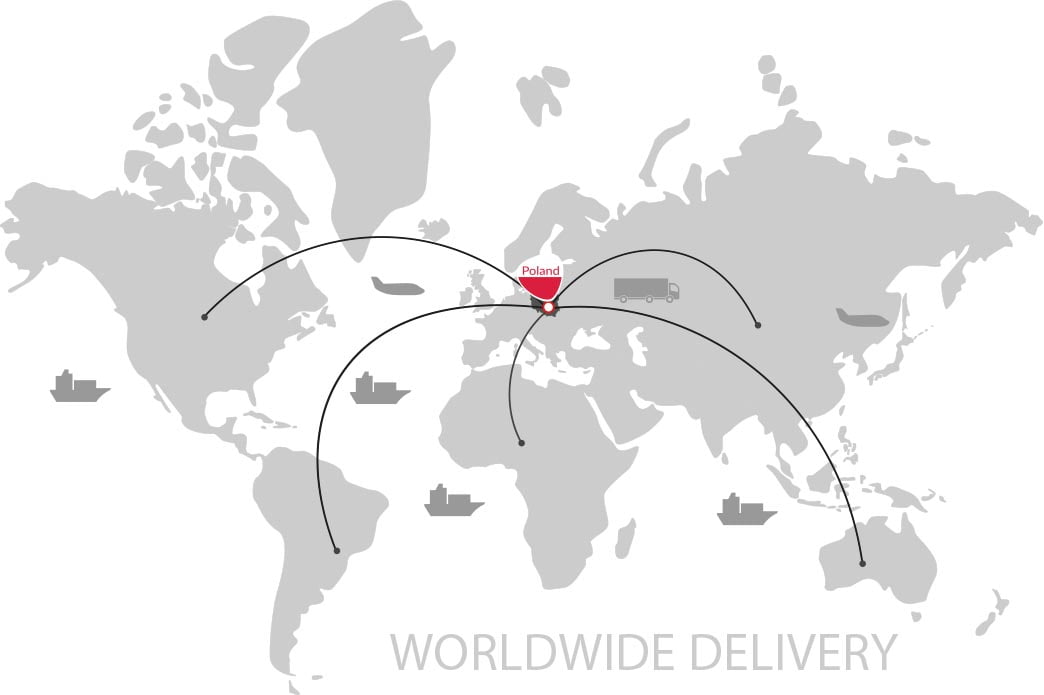
Prestressed concrete poles E type, produced by the LSW 2 – 54 line, are an excellent replacement for wooden and reinforced concrete energy poles. They are the future and their application is progress and modernity. They are product for the 21st century.
Comparing to wooden and reinforced concrete poles, they are characterized:
- Period of use min. 30 years with preservation of surface quality min. 10 years. The life expectancy of poles is up to 100 years
- Transferring much greater forces than wooden or reinforced concrete poles
- No need to use guy ropes so there are various possibilities of pole-top constructions
- Much greater resistance to environmental conditions, e.g. strong winds
- A diverse assortment of dimensions and strength classes
- Very low maintenance costs
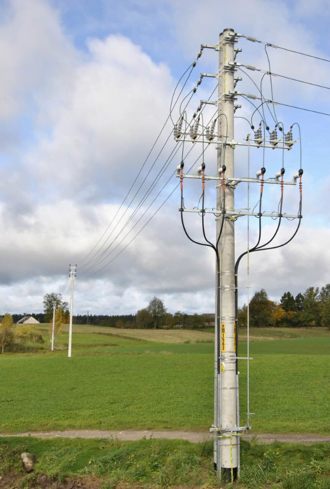
Our prestressed concrete poles transfer much greater forces than wooden or reinforced concrete poles, and thus are much more resistant to environmental conditions, e.g. strong winds.
This is due to the tensioning force, which is transmitted through the reinforcement basket inside the pole or more precisely through the prestressing reinforcement. This reinforcement is a set of prestressed steel wires according to ASTM A421, to which appropriate force was applied during the production process. The magnitude of this force together with the arrangement and the amount of prestressing wires and additional reinforcement is responsible for the value of the apical force transferred during the whole period of operation by the poles. The poles manufactured by our line comply with the CSA-A14-07 standard.
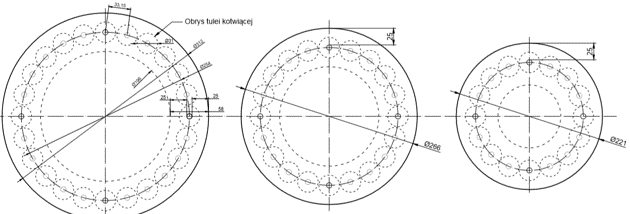
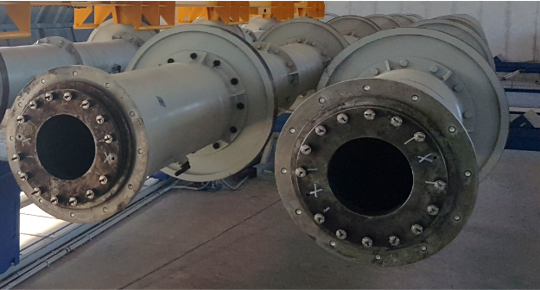
This is confirmed by strength tests according to CSA A23.1-14 / A23.2-2014
This test is carried out by applying a nominal force to the top of the pole and tempering. Another application of the force until the first scratch appears on the concrete surface.
Then increasing the bending moment leads to the destruction of the pole and confirmation of the expected value of the apical force, which can be safely transferred through the pole during the entire service life..
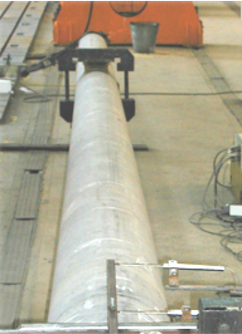
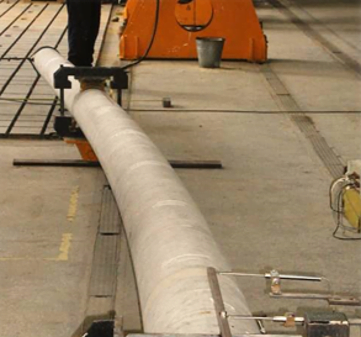
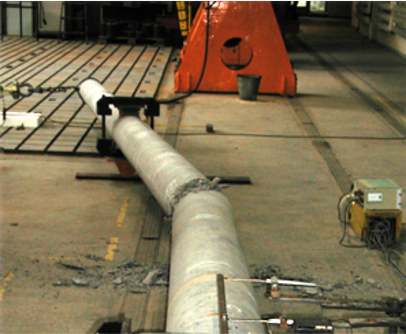
Thanks to the above, our poles have a much greater resistance to environmental conditions, e.g. strong winds than wooden or reinforced concrete poles.
What is extremely important in a socially crisis situation, our poles do not require any maintenance. It is not required to refresh or protect their surfaces with any substances or paints every year.
In connection with resistance to hurricane winds, they are practically maintenance-free element of the power network, because it is much faster to restore power line cables damaged by forces of nature than to additionally restore new poles.
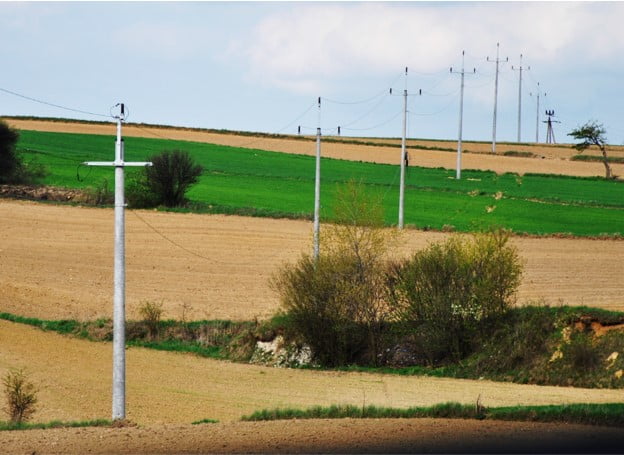
The excellent surface quality of our poles results from the use of non-collapsible instead of split molds, which additionally ensures shorter production time, attractive appearance and longer surface durability.
On the surface of our poles there is no seam resulting from the longitudinal split of the mold, so there is no place where calcium is leached from cement.
Depending on the client’s requirements, the reinforcement basket can be designed for the expected value of the apical force, thanks to which you can get a great variety of the assortment of dimensions and strength classes of poles for various applications. Moreover there is no need to use guy ropes.
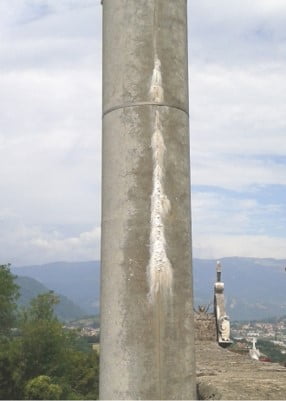
Surface with a seam
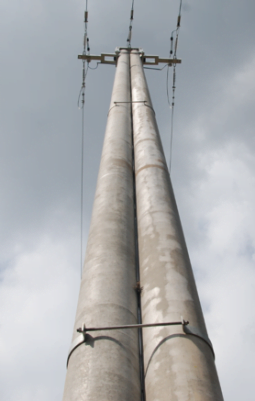
Surface of our poles without seam
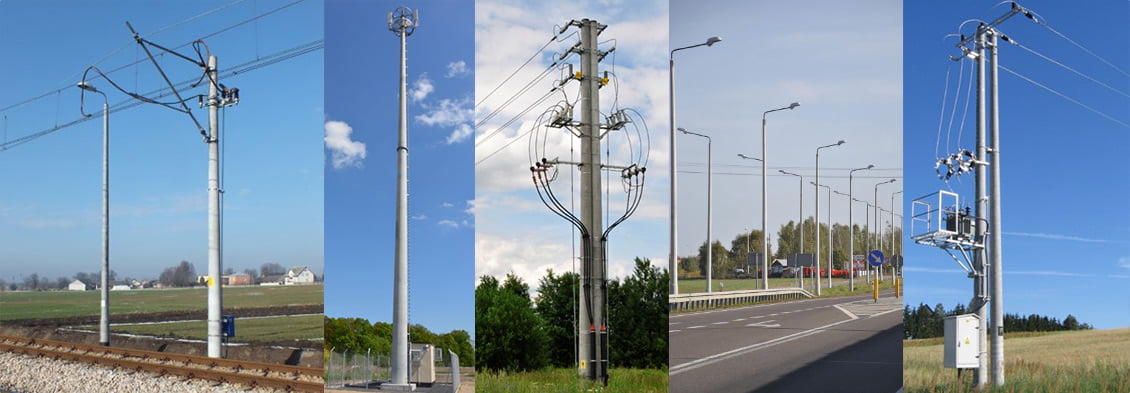
Our non-collapsible molds therefore increase the efficiency of the entire line.
The service of non-collapsible molds on the line takes place at their ends. There is no opening and closing of the molds so the production process can be much faster.
The process of filling our non-collapsible molds with a concrete mixture is very fast and involves entering the filling nozzle inside the mold.
Split molds must be unscrewed and filled from above and then screwed again. It takes time and affects the cost and efficiency of production.
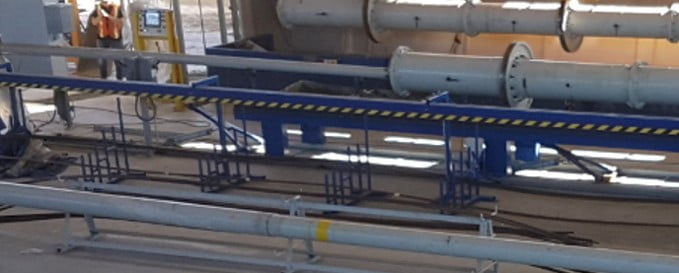
Quick entry of the filling nozzle into our non-collapsible mold
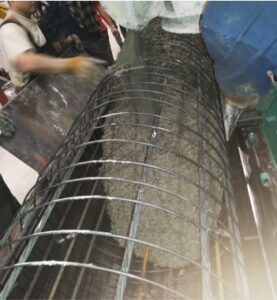
Filling the split mold from above
Dismantling poles from our non-collapsible molds is very easy and fast – by pushing out, while for split molds the whole mold must be unscrewed.
It takes much longer, affects costs, production efficiency and product quality.
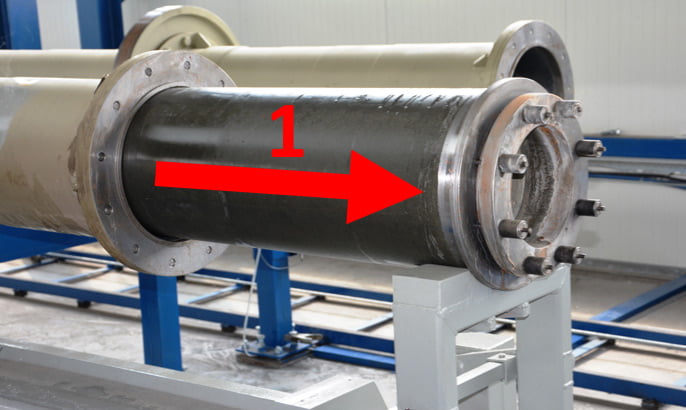
Fast pushing out of the finished pole from our non-collapsible mold
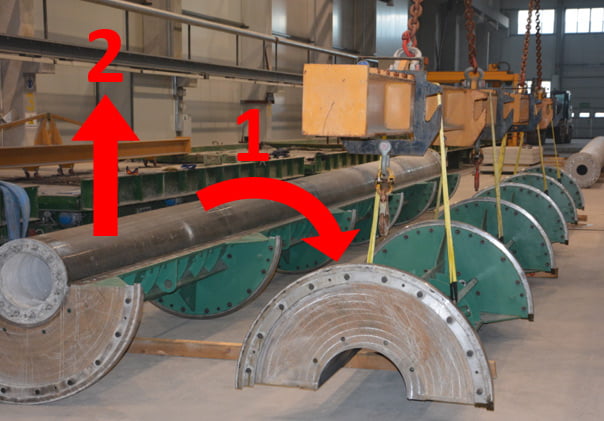
Two steps necessary to dismantle the split mold and take out the pole
Putting into our non-collapsible molds, reinforcement baskets and reinforcement tension takes place very quickly.
Another advantage of our non-collapsible molds over split molds is the lack of a connection line around the perimeter.
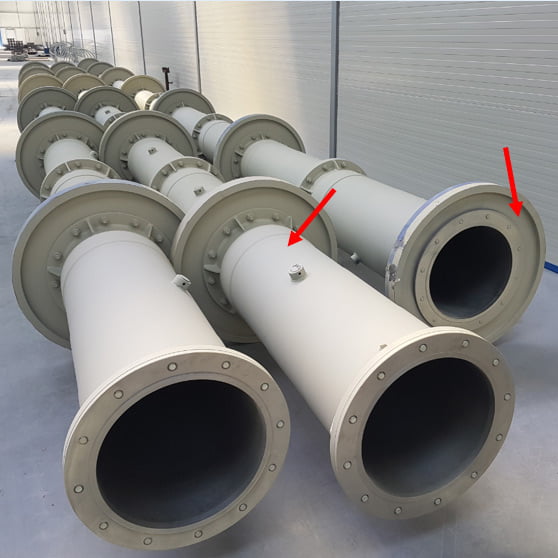
No connection line on our molds
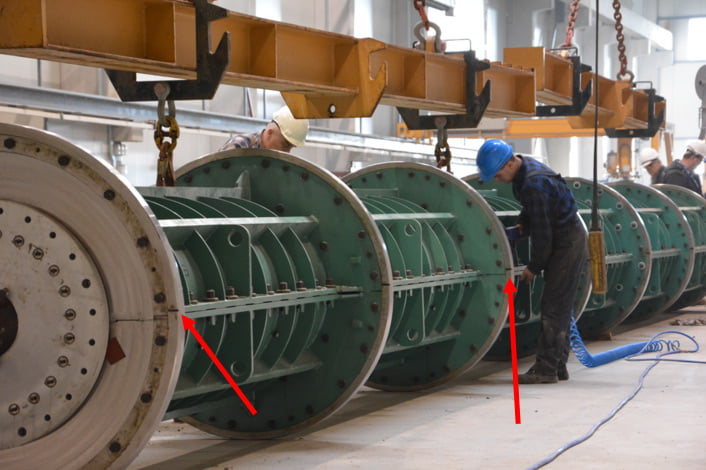
Connection line on the split mold on a rolling rings
Due to the lack of connection lines around the perimeter of our mold, the spinning process is smooth and silent.
Spin speeds can therefore be faster and the whole process shorter.
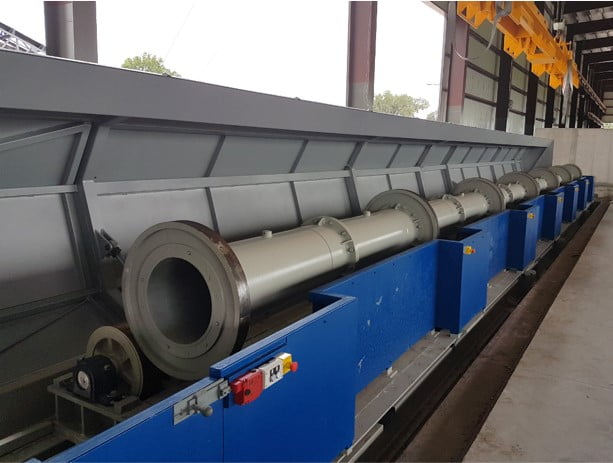
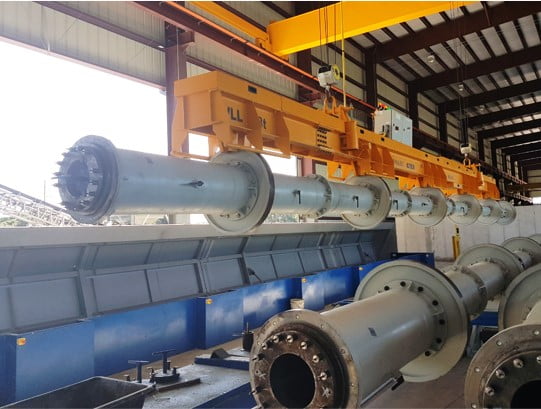
Based on over 20 years of experience, Strunobet Company always tries to adapt to the needs of a particular Client. Our priority is that the offer addressed to you, meet your expectations to the maximum.
We offer a whole family of LSW industrial lines with various capacities and expansion possibilities. This is possible thanks to the modular structure of the LSW line.
Understanding the dynamics and realities of the market, we can adapt a personalized offer not only for the new investments but also to existing industrial buildings for example old industrial halls.
If you decide to cooperate with us, you can count on:
- Close contact and technical advice from the very beginning. Contact is in English.
- A flexible and creative approach to the Client’s possibilities and expectations
- Constant supervision of the project supervisor over the entire investment period
- Service and warranty
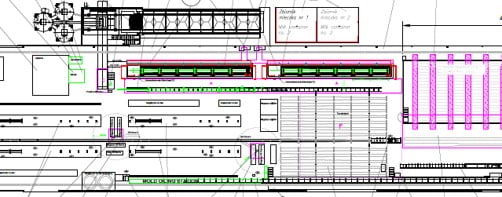
So what does the process of designing and realisation line looks like for a specific Client?
The LSW family line is actually a chain of interconnected device groups. It is a great mechanism that, when properly powered and operated, produces the final product – prestressed concrete spun poles.
The first step is to prepare a personalized offer for a specific customer.
Then we prepare the layout of the line in the constructed or existing hall.
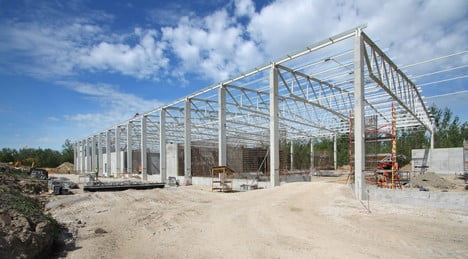
Groups of devices that make up the LSW industrial line.
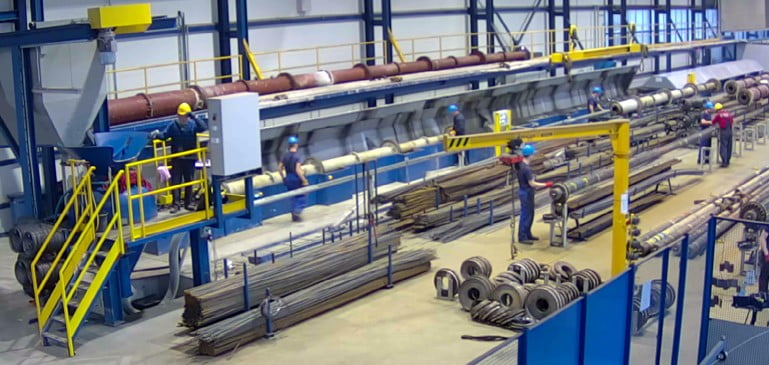
LSW 2 – 54 industrial line consists of 7 groups of machines, so these are:
- Filling group
- Spinners
- Curing chambers
- Fixing area
- Group reinforcement tension
- Dismantling group
- Transport and lubrication group
Our devices meet all safety standards and provide employees who operate them with the maximum level of ergonomics.
Each device within the operator’s working range is equipped with an emergency stop button.
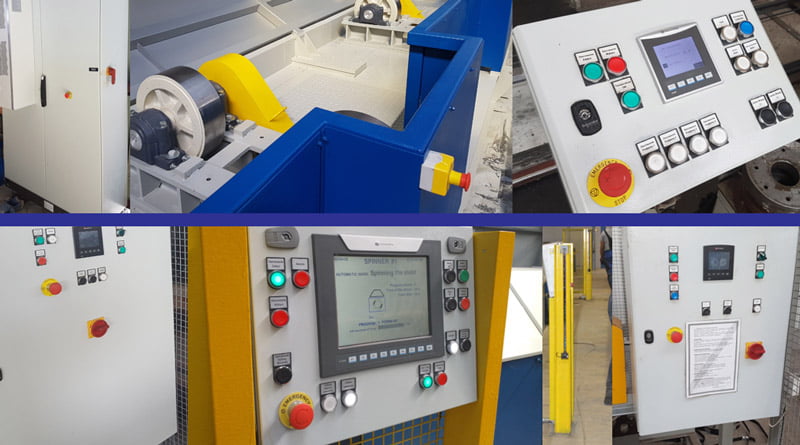
1. Filling group:
- Concrete conveyor from the concrete mix plant to the pump
- Concrete pump (commercial element)
- Concrete filling station with filling nozzle
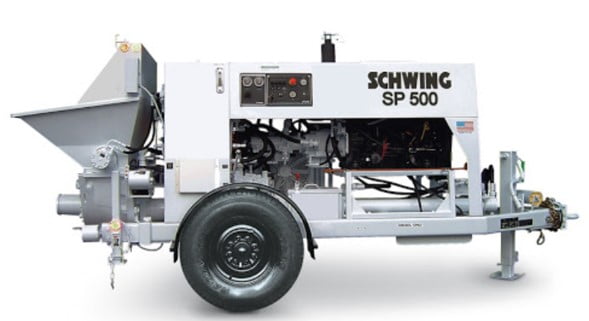
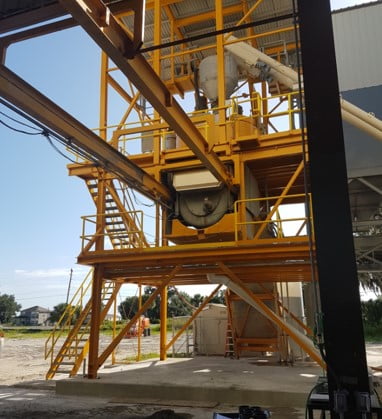
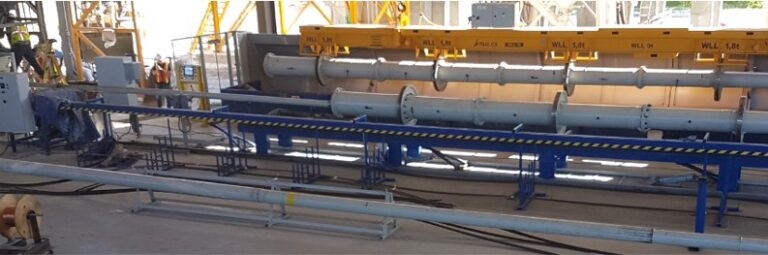

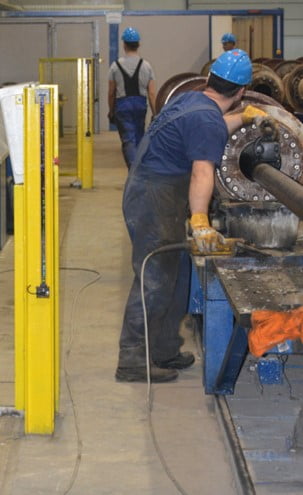
2.Spinners
- Spinner No. 1 in the basic or extended version
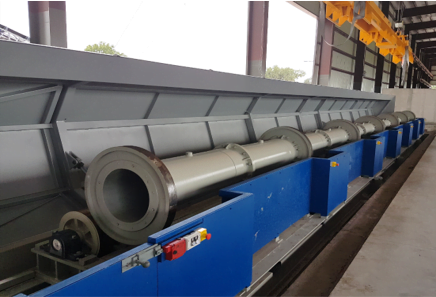
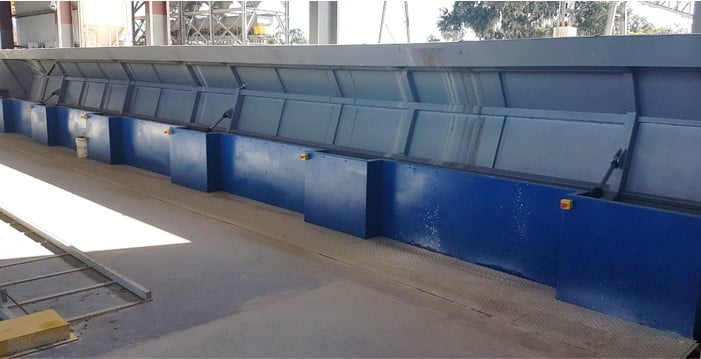
- Spinner No. 2
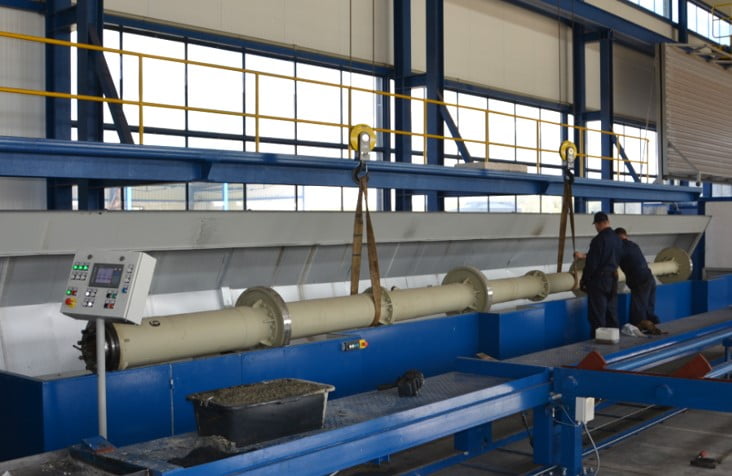
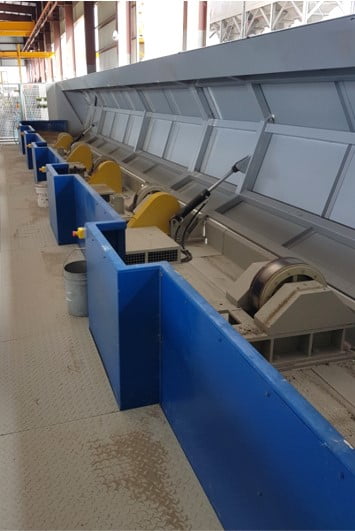
3.Curing chambers with an optional control system for the concrete curing process
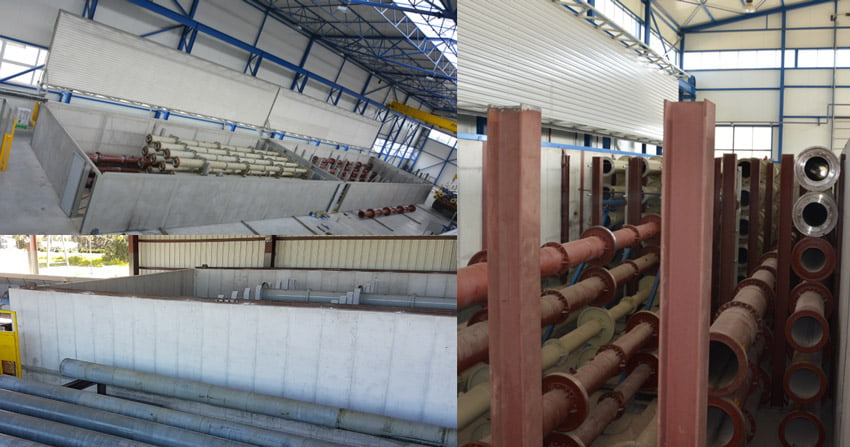
4.Fixing area
5.Group reinforcement tension
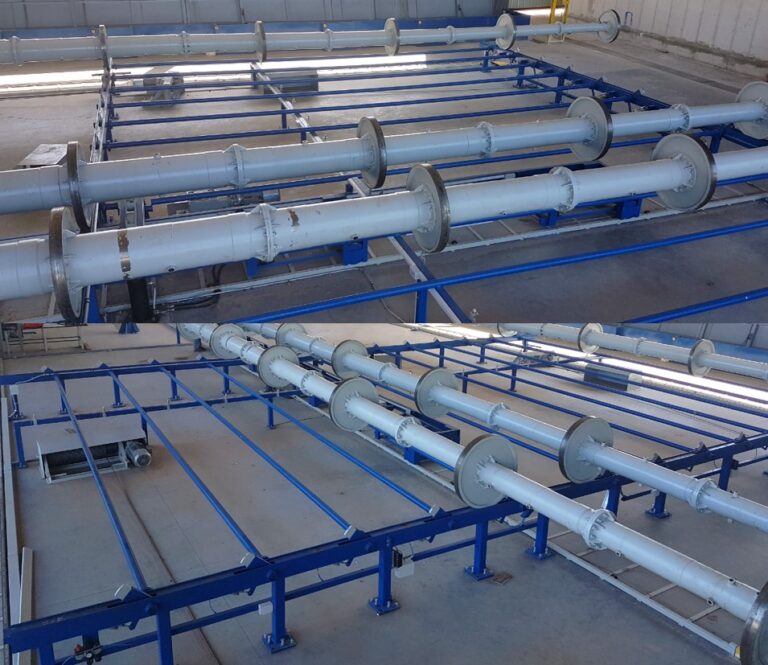
- Inclined track
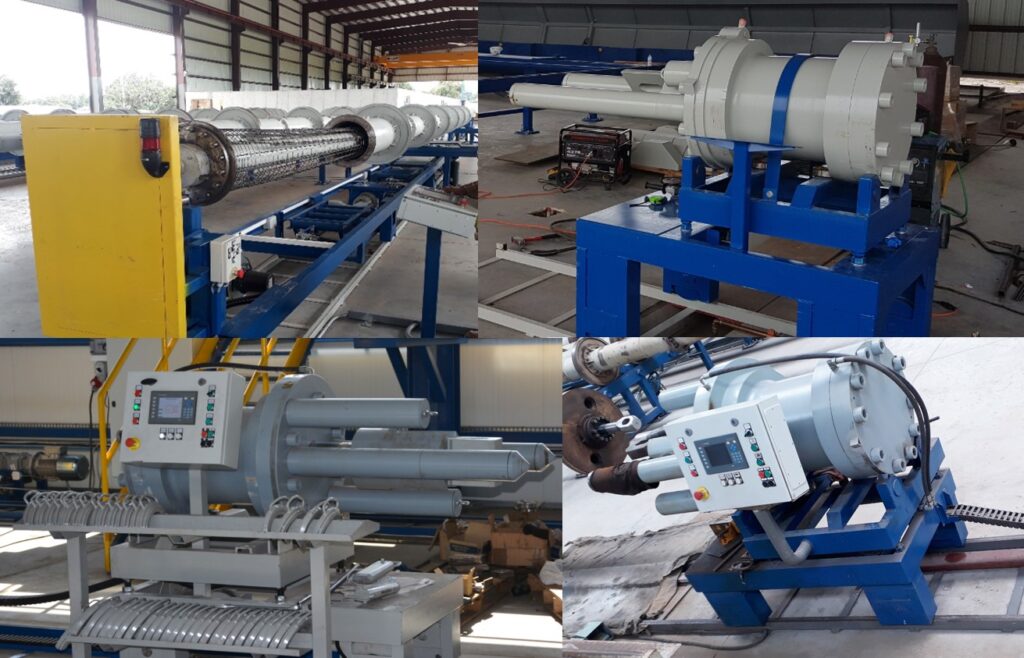
- Group tension hydraulic cylinder
- Trolley for putting reinforcement baskets to the molds
6.Dismantling group
7.Transport and lubrication group
All the machines working in line have electric, hydraulic or pneumatic drives.
Electric motors and hydraulic pumps (with electric drives) are controlled by inverters. This contributes to energy saving and longer life of the motors and other devices.
The electrical installation is designed in accordance with US standards.
Electrical cabinets are resistant to moisture and dust and also for drives working harder have air conditioning system to cool the interior.
- Lubrication station
Description of the process of implementing the offer for the Client.
When the production of equipment in Poland begins, we are in constant contact with the Client subcontractor for the construction.
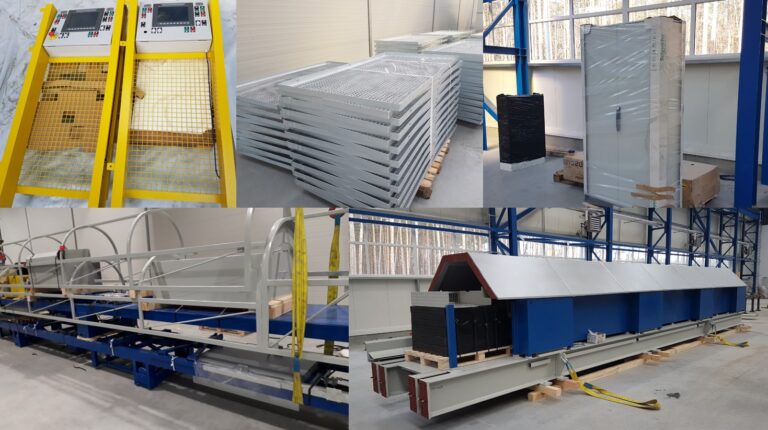
We verify with the subcontractor the location of connection points for powering machines and the correctness of execution of the foundations under spinners.
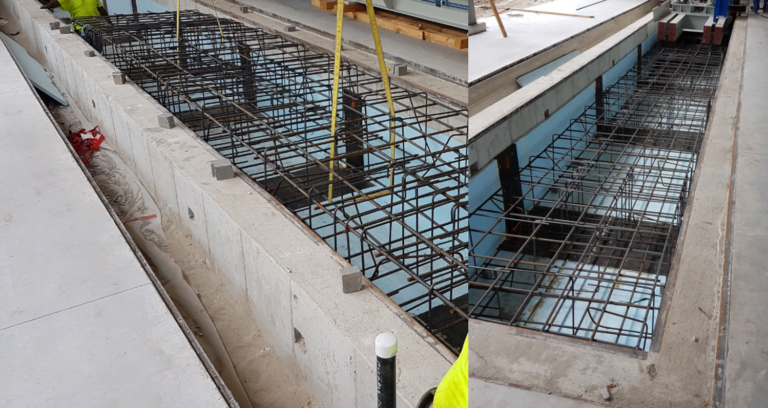
All machines from the line are successively sent by sea or land to the Client. Thanks to this, it is possible to start smoothly assembly process and first trainings on handling line devices at the Customer’s, even before the end of production of all equipment.
This results in a smoother investment implementation and Client safety from the risk analysis point of view.
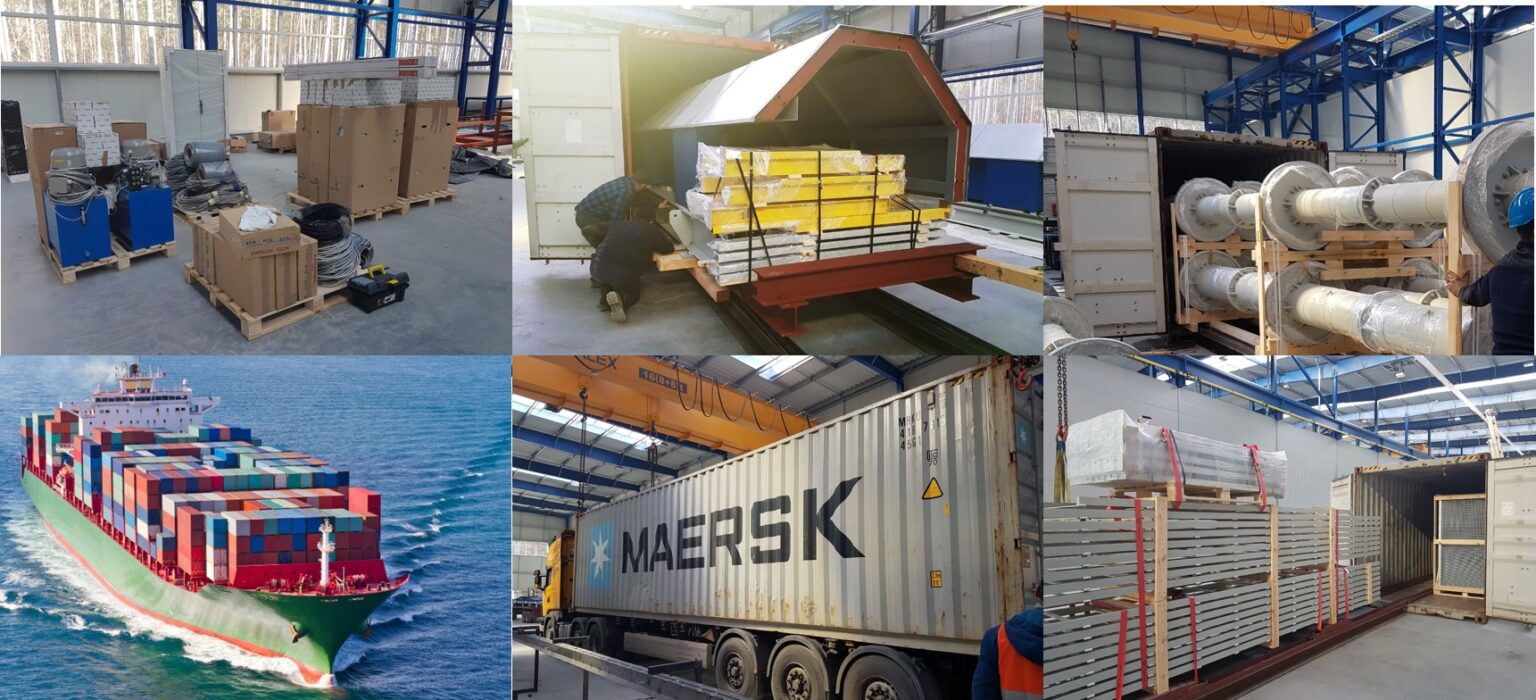
Installation and commissioning of the new line at the Client’s site is carried out by our qualified team.
Client employees trainings for line service are performed in English.
Full technical documentation of the line equipment (in English) is provided during commissioning.
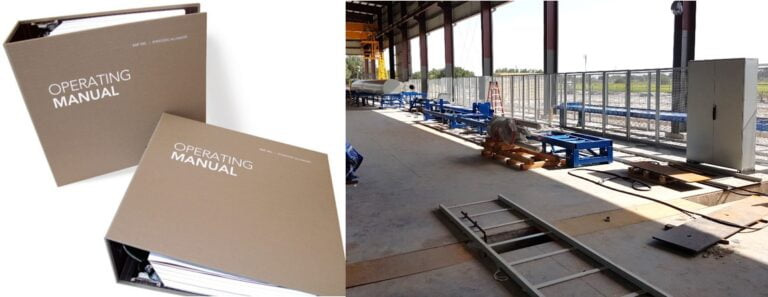
We supervise the operation of machines in line and support the Client during start of the production.
The Client’s training package also includes 2 free service visits. During these visits, the correct operation of all the machines is checked.
All necessary adjustments are made under the warranty.
We provide a warranty on the line and devices min. 12 months and 24 hours online service.
Service visits at Client’s factory.
We simply believe that only close relationships with the Client during the entire project and after its completion guarantee success.
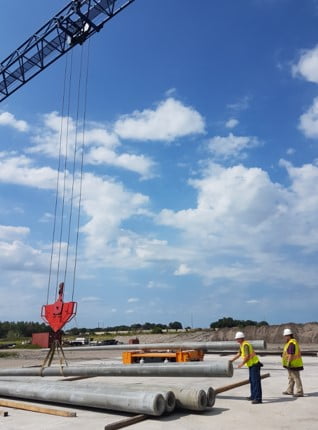