CONTAINER TRANSFORMER STATIONS
The company is the manufacturer of the system of container transformer stations in monolithic reinforced concrete enclosures. A modern production line allows for the production of a wide selection of stations, from the small-sized KSZ stations to large-sized KSW using the SCC self-compacting concrete with the compressive strength of C30/37. The production of enclosures does not involve vibrators and takes place in sealed steel moulds. The reinforced concrete castings are finished with painting and the external plaster in accordance with our customers’ requests. Then they are comprehensively fitted with electrical devices, including the transformer as well.
Container Enclosure Systems
In 2006, Strunobet-Migacz Sp. z o. o. launched an innovative technology of manufacturing concrete enclosures with the possibility of a wide range of applications. The enclosures and the transformer stations based on them meet all current production and safety standards.
Container Transformer Systems
Opracowanie zawiera modelowe stacje transformatorowe w obudowach kompaktowych KSZ, które pracują od zewnątrz oraz stacje kontenerowe w obudowach KSW, które są obsługiwane od wewnątrz.
Jeżeli wymagana jest inna konfiguracja, Strunobet-Migacz Sp. z oo oferuje fachowe doradztwo techniczne. Firma wykonuje przebudowy projektowe w zakresie budownictwa i elektryczności dla zatwierdzonych stacji.
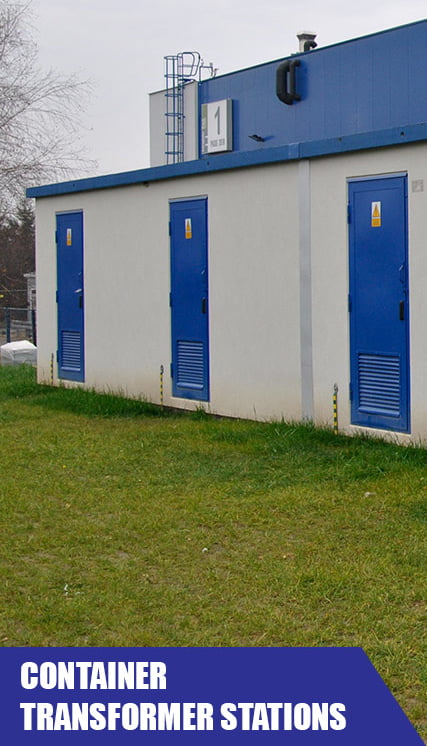
Fields of Application
The versatile technology allows the enclosures manufactured by Strunobet-Migacz Sp. z o.o. to be used in a wide range of applications.
The main application fields for reinforced concrete enclosures are::
- Professional Power Engineering
· MV cable joints and MV measuring gates
· container transformer stations operated from the inside and from the outside
· PZ and RS delivery-acceptance stations - Track Engineering
· container transformer stations
· track section cabins
· rooms for the supervision and management staff - Industrial Power Engineering
· high power capacity transformer stations
· enclosures of electricity generators
· rooms for the supervision and management staff - Individual designs upon customers’ requests
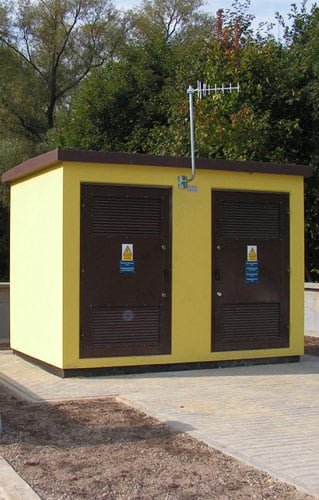
Innovative Manufacturing Technology
Manufacturing enclosures as monolithic components is a characteristic feature of the technology applied by Strunobet-Migacz Sp. z o.o. The container consists of independent components which are the cable of the basement, the main body and the roof. Depending on the equipment and field of application, the enclosures can be made as compact ones (operated from the outside) or container ones (operated from the inside).
Main body
The main body of the enclosure of a transformer station is a monolithic system of four walls and a floor. The floor separates the transformer and switchboard compartment from the inner space of the cable basement.
The transformer and the switchboard rooms are separated by a partition made from perforated or solid sheet in an angle frame. There is also an alternative of using a partition made of reinforced concrete slab fixed to external walls and the floor.
The enclosure is made from the SCC self-compacting concrete class C 30/37.
Casting of the enclosure is performed in an inverted position. The walls are cast together with the floor, which forms a solid monolith.
Openings for doors and grates are made in the main body while the openings for cables are made in the floor.
Inside, the walls are covered with white or other bright colour decorative acrylic plaster. Outside, the walls are also covered with acrylic plaster. The colours and types of elevation are offered in a standard version (see manufacturer’s catalogue). For the enclosure, it is also possible to use the colours and type of elevation according customer’s needs.
Increased degree of REI 120 protection is achieved by the use of PROMATEC plates fixed to the walls on the outside of the enclosure.
Cable Basement
The cable basement is made as a uniform prefabricated component with the dimensions adapted to the freezing zone of the ground, which constitutes the foundation of the station at the same time. The cable basement is made from the SCC self-compacting concrete class C 30/37.
The cable basement has a partition which is 300 mm high and is made in order to section off a part of the basement as a “bath” that can hold the entire (with some margin) oil from the transformer. Upon customer’s request, the partition can be as high as the basement and it can be made in the amount specified by them. The surface of the oil pit is covered with 2 layers of an oil-protective paint. The side walls have permanently cast in sleeves, such as plastic ones, which are cable and earthing penetration sleeves. On the surface, the exterior of the cable basement is covered with special bi-directional waterproof and oil-proof agents.
Roof
The roof of the enclosures is made as a rectangular reinforced concrete plank with variable thickness needed to form a 2.2% decrease in the direction of the bigger dimension. This edge requires the minimum thickness of the roof plank of 90 mm, and the maximum span in the middle of 130 mm. The roof plank is made from the SCC self-compacting concrete class C 30/37. Intricate components such as the roof verge or the eaves are additionally reinforced.
The roof is mounted directly on the walls. An elastomer background layer between the wall and the roof of the enclosure creates an air space which is a natural draft ventilation of the station. The roof is arranged freely. Therefore, in case of an arc fault it has the ability to go up, forming an outlet for the pressure and the post arc gases and particles, and then it falls freely to its former position.
The outer surface of the roof is painted with sun and rainwater resistant paint. Additionally, it can be covered with a layer of roof paper.
In order to adjust the shape of the roof to the architectural requirements, the overlays can be made in the form of double-pitched or pyramidal caps covered with tile sheets or ceramic tiles.